Building construction is a multi-faceted process in which multiple teams and stakeholders are involved. Separate architectural, structural, and mechanical models are brought together for the successful erection of a structure. So, when multiple stakeholders and models come together, clashes are bound to happen. For example, a beam can interfere with the HVAC unit, a pipe can interfere with the duct, and so on and so forth. If not resolved on time, these clashes can lead to rework during construction, resulting in significant project delays and cost overruns.
BIM Clash Detection helps save the hassle. By creating an integrated virtual 3D model of all the building components (architectural, structural, and MEP), BIM consultants help in early clash detection, making the entire construction process smooth and error-free.
What is Clash Detection in BIM?
Clash detection is a specialized process within building information modeling (BIM). It refers to the systematic identification, analysis, and resolution of design or placement conflicts during the pre-construction stage of building development.
Clashes occur when different building elements, systems, or components, such as architectural, structural, mechanical, electrical, or plumbing elements, intersect or overlap in ways that their placements are physically impractical or incompatible.
Earlier, a clash detection process was performed at the construction site. Not only was the process tedious and time-consuming, it also led to significant project delays. Today, Building Information Modeling has made the process extremely easy and cost-effective.
BIM experts leverage the power of Autodesk Revit to create individual and then a single federated 3D BIM model of various building trades, including architectural, structural, and MEP (mechanical, electrical, and plumbing). They then use Navisworks and other clash detection software to detect and resolve clashes/ overlaps that occur when these different building components intersect with each other.
Performing automated clash detection using NavisWorks during the pre-construction (the design) stage helps BIM MEP experts to resolve errors and clashes. It not only reduces manual efforts but also leads to minimal rework and delay during construction.
Different Types of Clashes
Most clashes during construction are divided into three main types: Hard, soft, and workflow clashes.
Hard Clashes
These are the physical conflicts that occur when two or more elements try to occupy the same space simultaneously. For example, a structural beam intersects with a duct.
Soft Clashes
Soft clashes result from indirect interference mostly between MEP components. It occurs when two or more elements create constructability or operational issues. For instance, a water pipe passes too close to an electrical conduit, making maintenance difficult or increasing the potential chances of a short circuit.
Work Flow Clashes
Also called 4D clashes, workflow clashes are mostly scheduling-related clashes and affect overall project efficiency. Examples of these clashes include workflow clashes, timeline and material delivery clashes, equipment delivery clashes, etc.
The Process of BIM Clash Detection
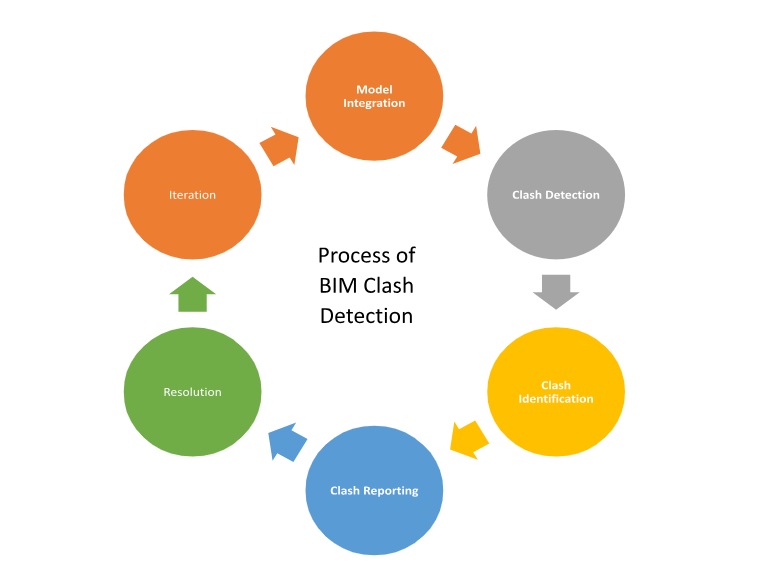
Model Integration
This is the first step in clash detection. It involves integrating the 3D models from various disciplines, including architectural, structural, and MEP BIM modelers using Autodesk Revit to create and merge different BIM models (structural, architectural, and MEP) into a federated BIM model, which represents the entire construction project.
Clash Detection
Once the models are integrated, specialized BIM software tools come into play. These tools, like Autodesk Navisworks, Revit, Revitzo, and Trible Connect, are equipped with powerful algorithms to analyze the 3D BIM model meticulously. The tools also help seamless collaboration among all stakeholders during clash resolution.
Clash Identification
The most common clash detection software is NavisWorks, which flags clash by pinpointing the exact locations and types of conflicts. These clashes range from structural elements conflicting with architectural features, MEP systems intersecting with structural components, or even clashes within the MEP systems themselves.
Clash Reporting
After identifying the clashes, the software generates a detailed clash report, detailing all identified clashes. Every clash is categorized and described to make it easy for project stakeholders to understand the nature of the conflict.
Clash Coordination /Resolution
Clash resolution is a collaborative process. Different project teams and stakeholders work together to resolve identified clashes. This involves creating standards and rules for resolution, redesigning, repositioning, or modifying the conflicting elements, ensuring they no longer obstruct each other’s functioning.
Iteration
Clash detection is not a one-time task. It’s an iterative process that continues throughout the design and construction phases. As new information becomes available or design changes occur, additional clash detection tests are performed to maintain clash-free models.
Benefits of BIM Clash Detection for AEC Professionals
Did you know by adopting BIM’s Clah Detection technology, architects, engineers, and consultants can save up to 70% of construction rework? But that’s not all. Here are some other benefits that make BIM clash detection and coordination a preferred choice of modern AEC professionals:
1. Early Clash Identification
BIM Clash detection allows for the early identification of conflicts and clashes in the project design phase. Architects and engineers can detect issues much before the construction actually begins; this enables proactive problem-solving and prevents costly rework onsite.
2. Higher Accuracy During construction and Onsite Installation
Pre-fab drawings extracted after 3D clash resolution ensure greater geometric accuracy, precise component manufacturing, and seamless onsite installation. This significantly reduces manufacturing waste and leads to faster and more accurate onsite construction.
3. Significant Time and Cost Savings
By addressing clashes during the design phase, projects can avoid expensive construction delays, change orders, and rework. This leads to significant cost and time savings over the course of a project.
4. Higher Onsite Safety
Clash detection helps identify safety-related clashes, such as conflicts between structural elements and egress routes. Addressing these issues enhances overall project safety.
5. Enhanced Collaboration and Coordination
BIM clash coordination encourages collaboration among different project stakeholders. Architects, engineers, contractors, and subcontractors can all come together and simultaneously work on the same model. It fosters effective communication and teamwork as well as reduces misunderstandings, errors, and disputes.
6. Maximum Quality Assurance
Resolving clashes ensures that the final construction aligns with the design intent. This leads to higher-quality buildings and structures that meet design specifications.
7. Reduced Project Disruptions
Coordinated Drawings minimize disruptions during construction. It reduces the likelihood of unexpected issues at a site that can cause construction delays and disruptions to the project schedule.
Accurate Cost Estimation and Bill of Materials (BOM)
Clash detection helps in accurately estimating construction costs by identifying potential issues that may require additional materials, labor, or design modifications.
Enhanced Client Satisfaction
Delivering projects on time and within budget while meeting design expectations leads to greater client satisfaction. Clients are more likely to recommend and work with firms that consistently deliver successful projects.
The Growing Demand for BIM Clash Detection Among AEC Professionals
AEC projects are getting increasingly complex and the demands for completing projects within defined timeframes and budgets are quickly increasing. This has led to the significant adoption of BIM clash detection within the AEC industry. By using a common data environment (CDE) and clash-free generative designing, BIM ensures superior coordination during building construction, with accurate BOMs, BOQs, and GFC drawings.
With Coordinated BIM models at their fingertips, AEC professionals can cut down on errors and rework that crop up during the construction stage. This helps them save installation time and budget significantly.
So, with progressing technology and increasing complexities in the AEC sector, the demand for BIM clash detection is destined to rise. Pre-construction resolution of clashes will soon become mandatory and not a matter of choice.
Want to unlock the benefits of BIM Clash Detection for Your projects? Contact us today to know how our Revit Clash Detection and Coordination Services can help you accentuate the speed and accuracy of your project.